I made this room last year, meaning to take pictures later on - and forgot to take the pictures.
I had made a kitchen room box for my granddaughter and thought it would be fun to make one for myself using some of my collection of Reutter miniatures. I had a hard time trying to mix a paint for the hutch to match the country blue Reutter sink cabinet, but in the end I came pretty close. I found some nice sheets of tile for the walls and floor on Ebay and Etsy.
For the white kitchen dresser on the back wall, I used a white Town Square triple dresser and made a hutch for the top.
Tuesday, June 2, 2020
Monday, June 1, 2020
Folk Art Kitchen Room Box
Years ago I bought a little set of wooden cookware. I thought it would be nice to use them in a folk art room box.
Years ago I made some clothespin dolls as Christmas tree ornaments, and thought I'd make some more someday. I even bought more clothespins to make them, but never got around it.
A couple weeks ago I finally got around to it.
The hearth is made of styrofoam. I've been recycling packing styrofoam into dollhouse projects. The chair started out as a rocker with a broken arm. I removed the other arm and the rockers, then painted the decorative motif. I also made the corner hanging cupboard, work table, wall shelf and towel rack.
Rio Lobo adobe room box
I think this is my 5th room box or dollhouse using styrofoam. One house was built of builders' foam, another was carved from a styrofoam block, the rest using styrofoam used to pack products shipped to my home.
My first choice to recycle my stack of styrofoam sheets was to make a southwest adobe house, but I just couldn't come up with a design I liked. Every plan I drew up wound up including a walled patio, a garden, etc., but I wanted to keep a more compact footprint. That's why I wound up making an Alpine style stone house.
I really liked the hearth in this one, and I had miniature chairs similar to those in another adobe house in the movie. Also, I had previously tried making an adobe brick wall using a woodburner on styrofoam which looked quite nice.
I decided to make a southwestern room box using styrofoam to simulate adobe brick walls. I had just enough 1/2" thick styrofoam for 3 walls, which I planned on gluing to 1/8" thick birch plywood. I had my walls all cut out when I ran into a problem. Using a piece of the 1/2" styrofoam that was left over, and taking woodburner in hand, I began to practice making the adobe bricks. It didn't work like it did last time. I was flummoxed till I finally realized that the styrofoam I used before was denser than the stuff I was using now. This time instead of nice delineating lines, I had a mess of deep gouges. I even went so far as to heat a palette knife over a candle, still too hot, still a mess. This is why I had to give up on part of my vision and go with smoothed out adobe walls. I must say, I was really disappointed.
I matched the wall color to a photo I found online of an old adobe wall, using a mixture of acrylic colors of a color called Georgia Clay, Camel, and Warm White. It looks too pink in these photos, much better in person.
The floor is meant to represent an adobe earthen floor that would have been waterproofed with oil. I used a plaster skim coat first, then painted the floor with a mixture of the clay color with Milk Chocolate and a touch of Asphaltum. The paints were all by Americana and Folk Art.
The hearth was carved from a block of styrofoam, and I made the cupboard from scratch. I took apart an unfinished Town Square table and redid it to make the kitchen table.
I started by putting the work table into the microwave and zapping it till the glue melted enough so that I could pull the pieces apart. I usually check my pieces every 10 seconds or so. I've done this quite a few times, and once a piece got too hot in the microwave and got badly singed.
Once the pieces were cool I sanded the glued areas smooth, then cut the bottom stringer to length and made a new table top, then glued the whole thing back together.
I used Stiffy fabric stiffener to make the curtain in the doorway and the one covering part of the cupboard's bottom half. I still need to make a work table for the right hand wall, then I'll be moving on to accessories, I've gathered quite a few already.
To make the indentations for the oven and fireplace I used my woodburner like a carving knife. Areas that lost a bit too much in the carving were filled in with drywall joint compound, then sanded gently till smoothed down. Since the oven and fireplace area were going to be painted black, it didn't matter if the backs of them were still a bit rough, as they wouldn't be noticeable.
In addition to the cupboard and kitchen table I also made a work table and a couple of small shelves. I wanted the linen towel drying on the rack to look damp and crumpled, so I dampened a one ply piece of facial tissue with watered down white glue, then carefully slipped it onto the rod and let it dry.
The rag rug in the corner of the room was one I found in my stash of older stuff I made. It was my first attempt at making one, and I stitched embroidery floss together with my sewing machine. Later I made another rug using an easier method by gluing the threads to a backing of gauze. Here's a link to that tutorial.
I needed some clay pottery for the room. I have assorted jugs and bowls in my stash, but all of them have a shiny glaze. What's a mother to do?
I turned to cheap wooden bowls bought at the craft store. First I sprayed them with Krylon matte finish to seal them, then I painted or colorwashed them in a clay color. When dry I sprayed them with more matte finish. One tiny bowl cracked, but after it dried it shrank back and the crack became barely visible.
I also used the matte finish spray to tone down the shine on another jug. The small jug on the kitchen table is still very shiny, but the bigger jug on the hutch counter was sprayed and looks quite different.
This picture shows a before and after version of a jug. I sprayed one jug with matte finish, then painted it. I liked the mottled effect on the jug I painted, so I left it with just one coat of paint. When it was dry I sprayed it with 2 coats of matte finish.
I'm very pleased with the way this next jug came out. I had some unfinished white vases that had just the right shape. Then I looked through my button can to find one that would make a nice lid with a handle.
covered them with a wash which was composed of a dab of milk chocolate colored acrylic paint thinned with a generous amount of water.
The Ceiling
To make the peeled log beams I started scruffing up a wooden dowel with my dremel, but after I painted on color washes of burnt sienna and gray, and smoothed down the raised wood fibers, (which didn't look good), I could barely see what I'd done with my dremel. I decided to just stick with the color washes.The sticks that form the rest of the ceiling were made by cutting bits off a whisk broom. I used a whisk broom to make a palm thatch roof for my Caribbean Cottage, and had part of a small broom left over. I gave a section of straw a coat of burnt sienna craft paint, then cut bits off to the correct length. To stick the straws to the ceiling, I thinned some white glue with water and brushed it onto the ceiling, a small section at a time.
Here's a picture with the acrylic front panel in place. I used the acrylic from a cheap poster frame that I bought with a 50% off coupon, and cut it to size with my Proxxon variable speed scroll saw.
Half Inch Scale Alpine Dollhouse
This is a dollhouse made mostly of recycled materials.
Last spring we had our bathroom remodeled, and wound up with a big pile of styrofoam sheets of varying thicknesses. It couldn't be recycled, and I didn't feel like breaking it into pieces and piling it all into our town trash bags at a cost of $4.00 a bag, especially since I had enough to fill at least 2 big bags. I decided there had to be a way I could use up at least some of it. I had recently built a dollhouse using rigid builders insulating foam, and decided I'd try and use the thicker styrofoam packing sheets for my next build.
I had recently been looking at charming pictures from the Disney movie Pinocchio, which inspired me to build an alpine style masonry house, since I had several large sheets that were up to 1 & 1/8" thick. That would translate into approximately 2 foot thick walls in half inch scale. My half inch scale house was to look like it was made of 2 foot thick stone covered in stucco.
I thought a barrel tile clay roof would be a perfect topper, especially since I'd heard of people using corrugated cardboard to build that style roof in miniature. We had a nice supply of discarded cardboard shipping boxes on hand.
Styrofoam packing sheets are composed of tiny balls pressed together, whenever you break up a piece of styrofoam you wind up with a mess made up of those little balls that stick to everything with static electricity.
First I had to be able to cut the sheets to size without making a huge mess. I have a Proxxon DS 115/E scroll saw which does a dandy job of cleanly cutting styrofoam. For cutting larger sheets or thicker pieces I used my bandsaw. I have in the past, used my electric carving knife, but it didn't make as clean a cut.
Another way of cutting the foam is by using a hot wire. I've included a picture of one because the first time I ever needed to cut foam I had no idea of what a hot wire looked like.
My problem with the hot wire was that I just couldn't cut a straight line with it. I've found it better for cutting foam to make slopes for miniature landscaping.
I learned that styrofoam can be sanded to shape or made smoother. I used fine grit sanding pads for this, always stroking in one direction, otherwise the styrofoam would start to crumble. I practiced on a few pieces to get the hang of it.
I started building by gluing the left hand and back walls to a birch plywood base using Weldbond glue. I'd used it on my builders foam project and it worked fine. Next I glued down a thinner sheet of styrofoam as a base for the floor. By the way, I didn't add the right hand wall till later on in the building process. For greater visual interest, I wanted to make a step up from one room to the other. I didn't have a piece of styrofoam the correct thickness to raise the floor level in one of the rooms, but I did find an old piece of foam board that was perfect for the job, so I used it to raise the floor that was eventually covered in boards.
I wound up using styrofoam wherever I could. The brick hearth was carved from a sheet of styrofoam. The little raised area within the fireplace was made from a little block of wood, as the styrofoam just wouldn't cooperate on a piece that small.
I wish I'd used a block of styrofoam to do the central hidden part of the staircase. No, I made a wooden staircase. Later I told myself I was an idiot, as no one would ever see the darn thing and why did I waste so much time on it?
Treating the styrofoam walls
I'd read somewhere that coating styrofoam with gesso would make the foam stronger, so I applied several coats to the walls. Later, somewhere else I read about applying a coat of MinWax Polycrylic finish.
The Polycrylic did an even better job, so I added 2 or 3 coats of that too, followed by a couple coats of acrylic paint. I was quite satisfied with the final strength, but discovered that the walls could still chip a bit on the corners. I decided to try applying a couple of thin coats of Weldbond glue to all the corner edges, and that seems to have solved the problem.
I've already posted about using corrugated cardboard to make the tile roof.
My other bit of recycling was the use of leftover bits of mat board to make the walls and ceiling of the second floor bedroom.
There's still a lot of styrofoam waiting for me in the attic.
I just remembered the stump house I made for my front yard gnome garden. I carved a solid block of styrofoam for that. I'll have to add a post about that one.
Here are two more pictures of the house.
Half Inch Scale Miniature Tile Roof from Corrugated Cardboard
The dollhouse this roof goes onto is a half inch, or 1:24 scale.
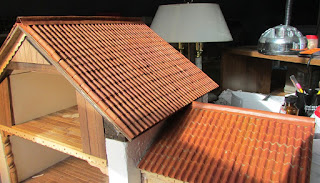
I cut up a corrugated cardboard box, then peeled off the top layer of paper. On the right you can see how it looked after I peeled the paper layer, on the left you see it cleaned up.
I cut up a corrugated cardboard box, then peeled off the top layer of paper. On the right you can see how it looked after I peeled the paper layer, on the left you see it cleaned up.
I used a skewer to pop the thin stuck on pieces,
and used a piece of fine sandpaper wrapped around a thin dowel to remove more bits of paper.
Once the furrows were cleaned up, I sanded the whole surface lightly, then removed the paper dust, bits and pieces with a brush.
After making a small sample roof piece, the next day I discovered it had warped a little bit. I'd glued the strips of peeled, corrugated carboard onto a piece of posterboard. In an effort to avoid warpage, I decided to try spraying both sides of my base cardboard layer with sealer. I used Krylon Matte Finish spray, I always have a can on hand.
Next I prepared strips to glue over the base layer, to form the rows of tiles.
I measured and cut 1 & 1/4" wide strips, then peeled off the paper backing. I found using a putty knife helpful to get the 2 layers apart.
Once I prepared the 4 roof panels I needed to glue them to the roof. The cardboard panels did tend to warp a little as they dried, so I did give them more sprays of sealer as I worked, and left each panel I was working on dry out overnight under a book. Some slight warping is adjustable by just gently bending the roof panels.
First I tried gluing a panel with spray adhesive. I was pretty sure it wouldn't work very well, but one can only hope for the best. It was not the best.
I pulled off the panel then started applying contact cement to the roof and the backside of the cardboard panel. I don't know why Weldbond can't make their applicator brush remain stuck to the lid so you can use it as you're meant to.
You can't adjust things when you use contact cement, once the pieces are glued together they're stuck, so you can't be making any mistakes.
The next day I found that the cardboard had popped up slightly at a corner and along one edge, so I slid a little strong glue in with a thin knife blade and clamped those spots down.
To make the tile roof cap I cut a strip from a brown paper supermarket bag and drew lines to represent the individual rounded tiles. Next I brushed white glue on the inner side of the strip, placed it glue side down onto a strip of plastic wrap, then shaped the paper around a thin dowel with the aid of a putty knife to define the crease. After sliding out the dowel I let the paper strip dry.
Once the strip had stiffened up I spread glue over the top strip of roof tiles on one side of the roof and placed the roof cap on top, pressing one edge to the glue coated tiles, then let dry. Once the strip was firmly glued on one side, I repeated with the other side.
The next step was coating the entire roof with a layer of white glue, giving the roof cap a couple of extra coats to make sure it was quite stiff and sturdy.
I used acrylic craft paints on the roof, a mixture of a clay color, raw sienna and burnt sienna.
I brushed on a section of the clay color, then while the paint was wet, I dipped the brush in a little raw sienna, brushed it on in random strokes, then dipped the brush in some burnt sienna and did the same thing. The trick is to let your wrist go free, sort of a whoosh whoosh stroke. The colors just blend together so you don't notice any strips of varying colors, but it doesn't look like you painted the roof all one color. Kind of hard to explain, but it's the best I can do.
After I saw this picture I noticed a missed a spot. I'll have to go back and give it a dab of paint.
By the way, I also put a dab of joint compound in the gap between the front and back sheets of tile under the roof cap, then painted it too.
Gnomes' Stump House Carved from Styrofoam
I started a collection of gnomes for my front garden a few years ago. You know how it is when you buy 2 or 3 of something just because you liked them, and then you find yourself buying more because they're just so cute, or pretty, or great or interesting looking. Well, I started finding gnomes that I really, really liked, and just kept buying them. At one point I thought it might be nice to add a stump house to my garden. I mentioned to my husband that there were a couple of fat logs out back that would make nice houses if only he'd drag one out for me to work on. He said fine, but never got around to it.
Eventually I started wondering if I could just make my own tree stump out of styrofoam. I'd made a stump house before, called the Nuthouse, by covering a tower dollhouse with styrofoam and a paper mache clay called Celluclay. That was however, an indoor tree stump house. I found someone selling larger styrofoam blocks on ebay and ordered one so I could make one that could sit outdoors.
This is the finished stump.
Eventually I started wondering if I could just make my own tree stump out of styrofoam. I'd made a stump house before, called the Nuthouse, by covering a tower dollhouse with styrofoam and a paper mache clay called Celluclay. That was however, an indoor tree stump house. I found someone selling larger styrofoam blocks on ebay and ordered one so I could make one that could sit outdoors.
This is the finished stump.
I placed a planter of silk ivy on top as it was early in the spring and nothing was growing outside yet.
I started by cutting the rectangular block into a round shape, then I took another piece of styrofoam to carve out a root which I glued to the stump. I used Weldbond glue for this and hoped it would stay in place even though it would be outside all summer. It held.
Next came carving the lump of styrofoam into bark. Years ago, when our oldest boy was 14, we gave him a woodburning set for Christmas. After he lost interest in it I put it away, and tada! some 28 years later I found a use for it. Yes, friends and neighbors, I carved the bark with a woodburning tool.
I painted the bark using several shades of watered down browns, applying them in washes, blending them while still wet. It took several coats, as each layer dried bits of white would show and I'd cover each section with more paint. Applying shades of color in washes gives you a more realistic effect in the end, rather than just flat out painting.
I made one mistake, which was not going out to buy some marine grade glue that would stand up to rain for attaching the balcony and little porch. I figured I'd take my chances with the Weldbond, which did last outdoors for several months. Eventually, however, part of the balcony fell down during a heavy rainstorm, and some of the little planks that formed the porch roof came unglued too.
It's alright, though. I have the pieces, and I just bought some Gorilla Glue and a low heat glue gun. One or the other should do the trick and get my stump house through another summer.
18th century Pennsylvania stone dollhouse
The first floor of the house is made of builders' foam, also known as foam board insulation. The board I used was green, just like the one shown below. It came in a 1" x 24" x 24" sheet, was inexpensive, easy to cut with a scroll saw and carvable.
My inspiration for this house was the photo below.
This is a photo of an old stone farmhouse taken sometime in the 1800's. The farm this house stood on is now part of urban Philadelphia, near what is now 17th and Dauphin streets. Similar houses were built throughout eastern Pennsylvania from around 1690 onwards.
Whitewashing of exterior walls was common. It was supposed to keep bugs out of the house and help preserve the stonework.
The door in the upper story was a common feature in homes of this era. This was so it would be easier to transfer stored items in and out of the building. Anything you can think of would be kept up there, even grain and lumber.
Closeup of the loft door. Usually they were plainer than this, but I saw a photo of one that I liked on a house that was rebuilt by a historical society, so I made my own version.
I added a little stone veranda. The stones were cut or torn from a cardboard egg carton, then colored with a series of paint washes. The moss between the stones is simply paint.
Here's a closer view of the stonework. Instructions showing how I did it are here.
I've furnished the house in an 1830's period.
The story that came to me was that the house belonged to a prosperous widow who decided she needed some peace and quiet and the house she was born in would be the perfect place, so she had it reroofed and made comfortable. Her sons and daughters said, "But Ma, won't you miss having us and all your grandchildren around you everyday?"
Back in her grandfather's day it could have sheltered a family of 6 or more.
Here's the main room of the house.
I've found that photos often make items in the foreground look oversized, so I retook the picture without the rocker. In real eye view the rocker looks just fine where it is. I decided to go for the invisible 4th wall look.
Here's the hearth and heart of the home, complete with ashes and a water pitcher and bucket in case a fire got out of hand (which they often did).
The other side of the room with a hutch displaying the homeowner's treasured china.
Here's a view of the inner side of the front door. All of the doors are fixed in place. The black iron hinges are clock hands. The latch here is also made using tiny clock hands.
Black slick Tulip brand fabric paint is very handy for black ironwork details. Recently, while working on another project, I discovered that I could form a shape with the stuff, then once it was dry, I could peel it off and glue it into place. Nice when you're trying to make a version of something and can't get it quite right the first time or two.
The bedroom with the height of luxury, a fireplace. As in any farmhouse of this era, it still continued to function as a storeroom.
Subscribe to:
Posts (Atom)